To properly regulate the flow of fluids in a system, choosing the right conuter valve is crucial. But with so many options on the market, it can be overwhelming to determine which valve best fits your application.
That’s why we’ve compiled a comprehensive guide to help you navigate the process of selecting the right conuter-valve. We’ll cover the factors to consider when choosing the right one for your needs. We’ll discuss the various materials and coatings used in the valve construction,
Additionally, for ensuring that your control valve is properly installed and maintained for optimal performance. Whether you’re a seasoned engineer or new to the world of conuter-valve, this guide is designed to equip you with the knowledge and tools necessary to make informed decisions when selecting a conuter-valve.
Easy Ways To Choose The Right Conuter Valve
Choosing the right conuter valve is crucial in any industrial operation. That’s why it’s important to have a guide to help you select the right one to ensure you get the best possible results. A conuter-valve is essential in regulating the flow of liquids or gases in a system.
It can prevent leaks and deliver the correct amount of fluid to the necessary areas. A guide can help you identify the type of valve you need based on your requirements. The guide can include information on the materials used to make the valve, the pressure ratings, and the temperature range that the valve can handle.
It can also guide the different types of seals and gaskets to ensure the valve is leak-free. Here are 8 steps to help you Chooser the right conuter-valve.
1. Identifying The Application And Process Requirements
When choosing the right conuter-valve, it is essential to identify the application and process requirements. Considering factors such as the type of fluid or gas being controlled, the pressure and temperature requirements, and the flow rate required.
Once these requirements have been identified, narrowing down the options and selecting the most suitable valve for the job is easier. One important consideration when choosing a conuter-valve is the type of actuation required.
Several different types of actuation are available, including manual, pneumatic, and electric. The choice will depend on factors such as the frequency of use and the level of precision required. Another factor to consider is the type of valve body material. Different materials have different properties and will suit different applications.
2. Valve Type And Functionality
When choosing the right conuter-valve, understanding the valvetype and functionality is crucial. Various computer valves are available today, each designed to perform a specific function. The most common counter-valve types include diaphragm, ball, gate, globe, and needle valves.
Diaphragm valves are ideal for controlling the flow of fluids and gases, while ball valves are excellent for applications that require quick on/off control. Gate valves are best suited for applications that require full flow control, while globe valves are perfect for applications that require precise flow control. On the other hand, needle valves are ideal for applications that require precise flow control in small lines.
3. Materials Of Construction
When selecting the right control valve, construction materials are a crucial factor to consider. Choosing the right materials will ensure the valve can withstand the process conditions and deliver accurate and reliable performance. The most common materials used for control valve construction include stainless steel, carbon steel, brass, and various plastics.
The selection of materials depends on the specific application and the controlled media, such as water, gas, or chemicals. If the media is corrosive, we prefer higher corrosion-resistance materials. Similarly, we choose materials that offer better wear resistance if the media is highly viscous. One of the key considerations when selecting materials is the temperature and pressure conditions of the process. High-temperature applications require materials that can withstand thermal stresses.
4. Valve Sizing And Cv Coefficient
Valve sizing and Cv coefficient are two crucial factors that play a vital role in choosing the right control valve. Control valves are handy in various applications, such as in the chemical and oil & gas industry, where they regulate fluid flow to maintain a constant pressure.
The valve size is determined based on the flow rate, which is calculated by considering the properties of the fluid, the pressure drop across the valve, and the required flow rate.
The Cv coefficient is a measure of the valve’s ability to control the flow of fluid, and it is calculated by dividing the flow rate by the square root of the pressure drop. Choosing the right control valve is essential for optimal system performance. A too-small valve will not be able to handle the required flow rate, resulting in pressure drops and reduced efficiency.
5. Actuation And Automation
Actuation and automation are essential in modern industrial processes as they help to improve efficiency and reduce labor costs. One crucial component in such processes is the control valve, which regulates the flow of fluids or gases. Choosing the right control valve is critical to the success of any industrial application.
One of the most common control valves is the conuter-valve, which offers accurate flow control and is highly reliable. When you select the right counter-valve, you need to consider several factors. Firstly, evaluate the process conditions, including temperature, pressure, and flow rate.
This is crucial in determining the valve material, size, and type. Secondly, you should also consider the mode of actuation, whether manual, electric, or pneumatic. Electric and pneumatic actuation provides greater control and automation, making them suitable for high-pressure and temperature applications.
6. Maintenance And Serviceability
Maintenance and serviceability are crucial factors when choosing the right control valve. A control valve is a critical component in many industrial processes and must be reliable and efficient. However, we must also ensure we can easily maintain and service the valve.
When selecting a control valve, various factors must consider, such as the type of fluid being controlled, the operating conditions, and the application requirements. One of the primary considerations for maintenance and serviceability is the valve’s design.
Choosing a valve that is easy to dismantle and reassemble for routine maintenance and repairs is essential. Additionally, the availability of spare parts and the ease of obtaining them is critical. A well-designed valve should have clear instructions and documentation to support quick and efficient maintenance procedures.
7. Compliance And Certifications
Compliance and certifications should be top priorities when choosing the right conuter-valve for your business. These factors ensure your equipment’s safety, efficiency, and reliability. First and foremost, you need to identify the specific regulations and standards that apply to your industry and location.
For instance, if you operate in a hazardous environment, you may need counter-valves that comply with OSHA or EPA regulations. Likewise, dealing with food or pharmaceutical products may require valves that meet FDA or NSF standards.
Once you have identified the applicable compliance requirements, you can look for certified products that meet or exceed these standards. A reputable manufacturer should provide detailed documentation of their certifications and compliance testing results.
8. Budget And Cost Considerations
When choosing the right conuter-valve for your application, there are several budget and cost considerations to remember. Firstly, it’s important to determine the amount of funding available for the valve purchase. This will help narrow down the options based on cost and affordability.
Additionally, you should also consider the long-term costs associated with the valve. This includes maintenance, repair, and replacement costs over time. Choosing a valve that requires minimal maintenance and has a longer lifespan can ultimately save money in the long run. Another factor to consider is the accuracy and precision required for the application.
High-precision valves may come at a higher cost but may be necessary for certain applications where accuracy is crucial. On the other hand, a less precise valve may be suitable for applications where the level of precision is not as critical.
9. Installation And Maintenance Considerations
When choosing the right control valve for your system, it’s important to consider installation and maintenance considerations. The first step is to evaluate your system’s requirements and select a valve that meets those needs. This includes flow rate, pressure, temperature, and fluid properties.
Once you have identified the appropriate valve type, it’s important to consider the installation process. This includes factors such as valve size, orientation, and mounting options. Ensuring proper alignment and connection to the piping system is also important.
In addition, consider the accessibility of the valve for future maintenance needs. The valve should be located in a place that allows easy access and inspection. Proper maintenance is crucial to ensure optimal performance and longevity of the valve. This includes routine inspections, cleaning, and repairs as needed.
10. Common Mistakes To Avoid When Choosing A Conuter-Valve
Choosing the right conuter-valve for your business can be daunting, especially if you are unfamiliar with the different types available on the market. However, there are common mistakes that you should avoid when making your selection. Firstly, you should avoid choosing a conuter-valve solely based on price.
While it may be tempting to go for the cheapest option, it could cost you more in the long run if the valve fails or needs frequent repairs. Secondly, you should avoid choosing a valve without considering the specific needs of your business.
You should consider factors such as the fluid or gas being transported, the flow rate, and the pressure. Failure to consider these factors could result in choosing a valve unsuitable for your business needs.
Conclusion:
Choosing the right conuter valve may seem daunting, but with the right information and research, you’ll find the perfect match for your needs. Consider the flow rate, working pressure, materials, and other important factors.
Don’t be afraid to consult with an expert or contact the manufacturer for guidance. With the right conuter-valve, your system will run smoothly and efficiently, and you’ll be the envy of all your valve-loving friends.
By meticulously evaluating the application requirements, valve types, materials, sizing, actuation, and budget considerations, organizations can make well-informed decisions that lead to smooth operations, cost-effectiveness, and enhanced productivity in their industrial processes. Choosing the right control valve is fundamental to achieving seamless and reliable process control, benefitting businesses across various industries.
FAQ:
[rank_math_rich_snippet id=”s-b95d3723-6835-4663-a5f8-0da54a1a958e”]
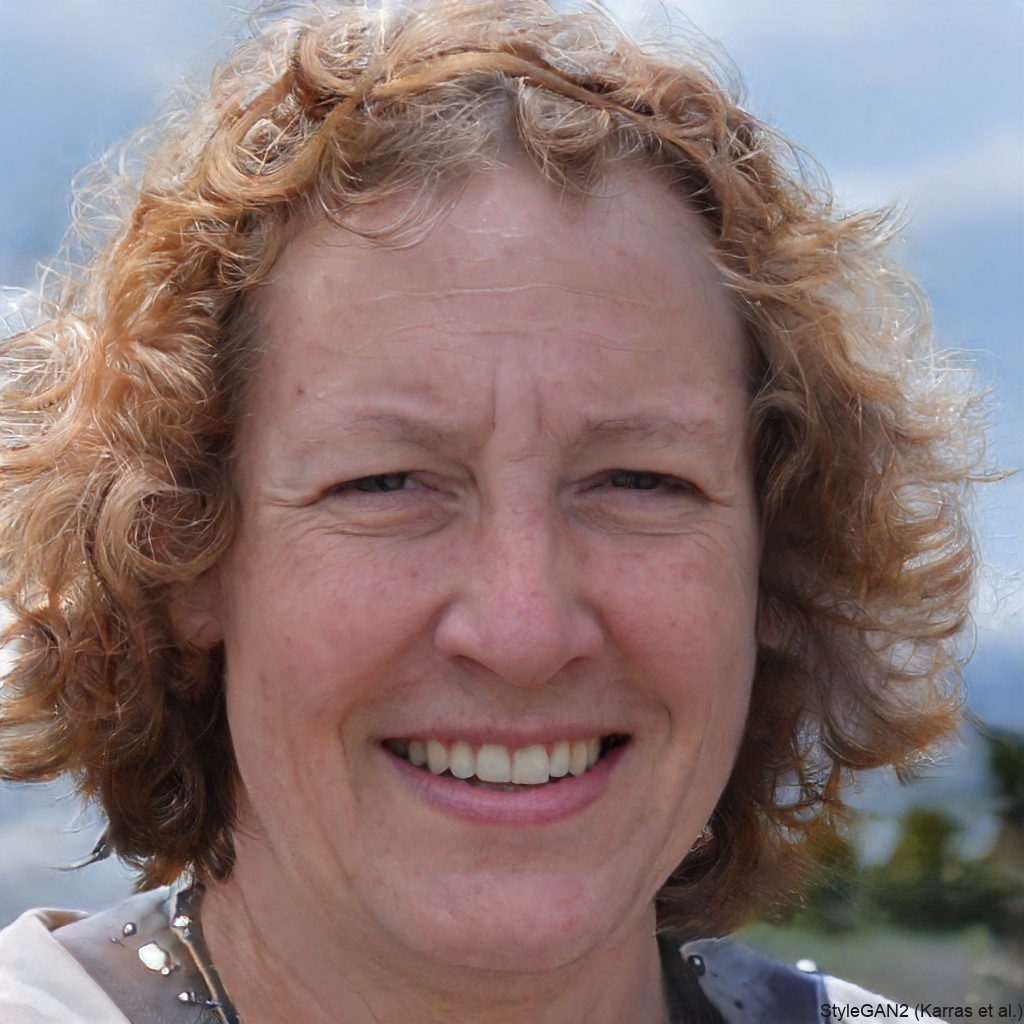
I am passionate about home engineering. I specialize in designing, installing, and maintaining heating, ventilation, and air conditioning systems. My goal is to help people stay comfortable in their homes all year long.