As a professional contractor or DIY enthusiast, you understand that a strong and stable subfloor is the foundation for any successful flooring installation. If you’re looking to install a hardwood, tile, or laminate floor in your home or commercial space, mastering the art of 3 4 sub floor installation is absolutely essential.
The 3 4 subfloor is a common type of subflooring that provides excellent stability and durability. But achieving a smooth and level surface requires skilful installation techniques and careful attention to detail.
In this blog post, we’ll explore the key elements of mastering the art of 3 4 subfloor installation. From prepping the subfloor to laying the panels, we’ll provide expert guidance to help you achieve professional results.
Installing Process Of 3 4 Subfloor
Installing a 3/4 subfloor is an important step in the construction or renovation process of a building. The installation involves several key steps to ensure a sturdy and level foundation for the finished flooring. Here’s a brief overview of the installation process of a 3/4 subfloor:
- Prepare the space: Before installing the subfloor, ensure the space is clean, dry, and free from any debris or obstacles that could interfere with the installation process.
- Measure and cut the subfloor panels: Measure the dimensions of the space and cut the subfloor panels to fit accordingly. Leaving a small gap between panels is important for expansion and contraction.
- Install the first row: Start by installing the first row of subfloor panels along one wall, ensuring they are flush against each other and properly aligned.
- Secure the panels: Use screws or nails to secure the panels to the floor joists, following any specific manufacturer guidelines for fastening.
- Continue with subsequent rows: Repeat the process for subsequent rows, ensure fastening each panel securely ed and properly aligned with adjacent panels.
- Fill gaps and seams: Once all panels are installed, fill any gaps or seams with wood filler or caulk to create a smooth surface.
- Sand and level: If necessary, sand down any uneven areas and use a levelling compound to ensure a flat surface for the finished flooring.
Remember, it is important to consult local building codes and regulations when installing a 3/4 subfloor, as requirements may vary depending on location and intended use of the space. Additionally, it is always recommended to seek professional assistance if you are unsure about any aspect of the installation process.
Which 3 4 Sub Floor Should You Choose
When selecting a 3 4 sub floor, consider the type of flooring you’ll install. Plywood is a popular choice due to its strength and durability. OSB is more affordable but not as strong. Consult professionals or follow manufacturer recommendations for the best subfloor for your project.
To ensure a successful 3 4 subfloor installation, the first step is to choose the right type of subfloor material. Plywood and OSB are two common choices, each with advantages and considerations.
The Importance Of Choosing The Right Subfloor
Choosing the right subfloor is crucial to structural integrity and longevity. A subfloor is a foundation for the finished flooring, providing stability and support. The 3/4 subfloor, plywood subflooring, is popular due to its strength and durability. It is made from multiple layers of wood veneers glued together, creating a solid and stable base for various flooring materials.
The thickness of 3/4 inch ensures that the subfloor can withstand heavy loads and resist movement or warping over time. Whether installing hardwood, laminate, or tile flooring, a 3/4 subfloor is an excellent option to provide a reliable foundation for your space.
Factors To Consider In Choosing The Right Subfloor
When choosing the right subfloor, several factors need to be considered. One of the most important factors is the type of flooring installed on top of the subfloor. Different types of flooring have different requirements in terms of subfloor materials and thickness. You should consider the moisture level where you will install the subfloor.
A moisture-resistant subfloor material may be necessary to prevent damage if the area is prone to moisture or humidity. Additionally, we should also consider the condition of the existing floor.
If there are any structural issues or unevenness in the current floor, additional measures may be needed to ensure a stable and level surface for the new subfloor. Choosing the right subfloor involves evaluating these various factors and selecting a material and thickness that will provide a solid foundation for your chosen flooring.
Plywood Subfloor: Pros And Cons
Regarding subfloors, plywood is popular due to its versatility and durability. A 3/4 inch plywood subfloor offers several advantages. Its thickness provides stability and reduces the risk of sagging or flexing over time. This makes it an excellent choice for supporting heavy loads and ensuring a solid foundation for flooring materials such as hardwood or tile.
Additionally, plywood is moisture-resistant and can better withstand humidity fluctuations compared to other subfloor materials. However, there are some drawbacks to consider. Plywood can be more expensive than alternative options, requiring careful installation to prevent gaps or unevenness.
Furthermore, plywood can swell or warp if exposed to excessive moisture or water damage. Despite these considerations, a 3/4 inch plywood subfloor remains popular for its strength and reliability in providing a sturdy base for various flooring applications.
OSB Subfloor: Pros And Cons
OSB (oriented strand board) is a popular choice for many homeowners regarding subfloors. Manufacturers bond wood strands with resin and compress them under high pressure to make this engineered wood product. One of the main advantages of using an OSB subfloor is its strength and durability. It can withstand heavy loads and provide a stable base for various flooring materials.
Additionally, OSB is relatively inexpensive compared to other subfloor options, making it a cost-effective choice for many homeowners. However, there are also some drawbacks to consider. OSB is more susceptible to moisture damage than plywood, and if exposed to water for extended periods, it can swell and lose its structural integrity.
Furthermore, OSB may not be as smooth or flat as plywood, making installation more challenging. Overall, while an OSB subfloor has advantages in terms of strength and affordability, it’s important to weigh the pros and cons before making a final decision.
Particleboard Subfloor: Pros And Cons
Particleboard subfloor is a commonly used material in construction, known for its affordability and ease of installation. They compress wood particles with resin and form them into large sheets.
One of the main advantages of particleboard subfloor is its cost-effectiveness, making it an attractive option for those on a budget. Additionally, the particleboard subfloor provides a smooth and even surface for installing flooring materials such as carpet, laminate, or vinyl.
However, it is important to consider some potential drawbacks when using particleboard subfloor. It has lower strength and durability than plywood or OSB (oriented strand board), which may result in sagging or warping over time.
Particleboard is also susceptible to moisture damage, so precautions should be taken to protect it from water exposure. Overall, particleboard subfloors can be suitable for certain projects, but weighing the pros and cons before deciding is important.
Installation And Maintenance Tips For Subfloors
When installing a subfloor, it’s crucial to choose the right material, such as plywood or oriented strand board (OSB). Plywood is preferred for its strength and durability. Ensure a clean and level surface free from debris and moisture. Secure the subfloor to the joists using appropriate fasteners and staggering seams for stability. Lastly, follow manufacturer guidelines for installation and maintenance.
Advantages Of Using A Combination Of Subfloors
Using a combination of subfloors, like plywood and cement board, offers increased stability and durability for your flooring. Plywood subfloors are valued for their strength and moisture resistance, while cement board is recommended for moisture-prone areas. If you properly install and level the subfloor, you can create a robust base for your flooring by combining both.
Cost Comparison Of Different Subfloors
When considering subfloors, there are various options to choose from. Plywood subfloors are a popular and affordable choice known for their durability. Another cost-effective option is OSB subfloors, which provide strength.
For superior moisture resistance and strength, AdvanTech subfloors are a premium choice. A cement backer board offers excellent water resistance and is commonly used in moisture-prone areas like bathrooms. The cost of each subfloor type may vary based on project size and location.
Conclusion
Choosing the right subfloor is crucial for the success of your flooring installation project. Each subfloor type has pros and cons, so it’s important to consider factors such as durability, moisture resistance, and cost before deciding. Additionally, proper installation and maintenance are key to ensuring the longevity and performance of your subfloor.
If you’re unsure which subfloor is best for your needs or need more information on installation and maintenance tips, consult our experts for guidance. Remember, investing in a high-quality subfloor will provide a solid foundation for your flooring and contribute to your space’s overall beauty and functionality. We have provided bulk information for 3 4 sub floor and hope our information was helpful from your perspective.
Frequently Asked Questions
[rank_math_rich_snippet id=”s-85f040b3-6294-469f-9bc6-79f120414d40″]
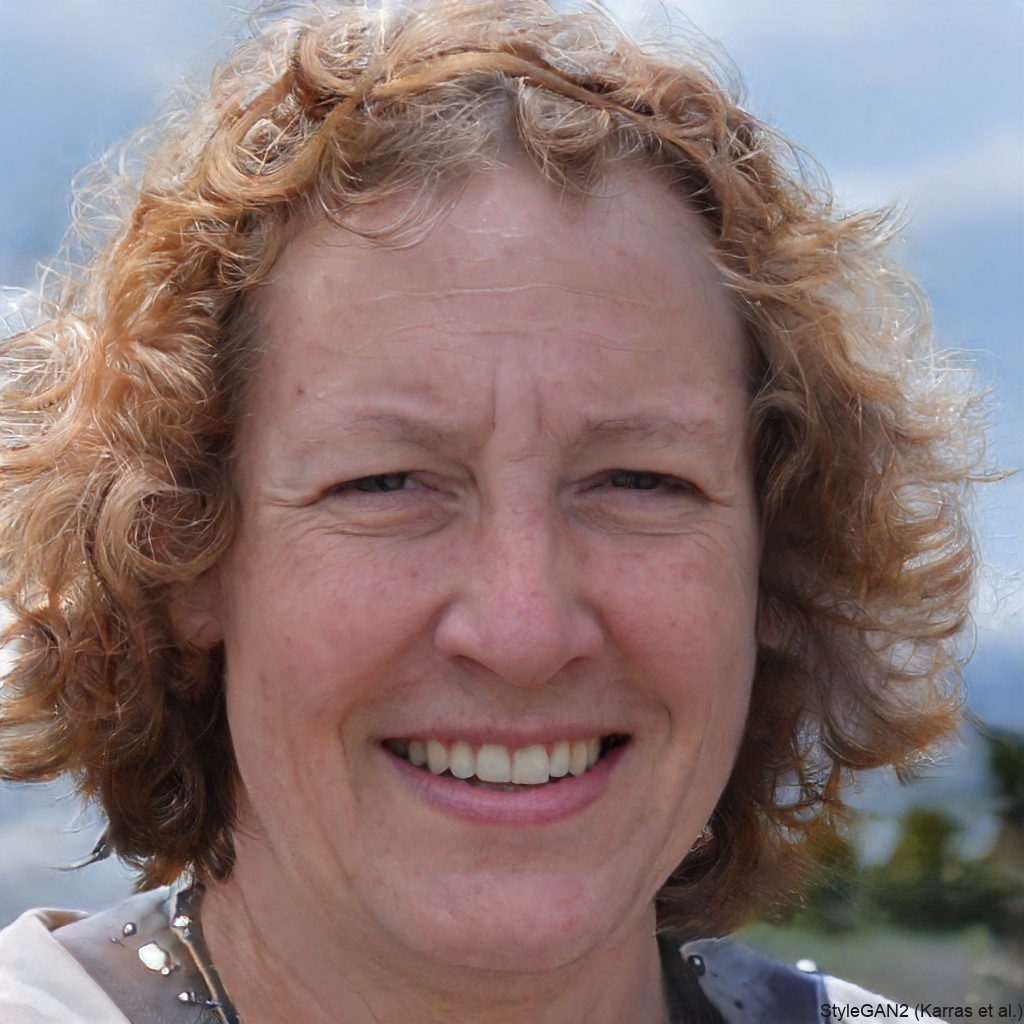
I am passionate about home engineering. I specialize in designing, installing, and maintaining heating, ventilation, and air conditioning systems. My goal is to help people stay comfortable in their homes all year long.