An air compressor 15 cfm at 90 psi is a powerful machine in various industries and applications. It is a device that converts power from an electric motor, diesel engine, or gasoline engine into potential energy stored in compressed air.
This compressed air powers pneumatic tools inflates tires, and even provides breathing air to divers. The 15 cfm (cubic feet per minute) rating refers to the air the compressor can deliver at a specific pressure, in this case, 90 psi (pounds per square inch).
This makes it ideal for applications that require a high volume of air, such as sandblasting, spray painting, and powering impact wrenches. Due to their efficiency, versatility, and reliability, air compressors have become an essential tool in many industries, including automotive, construction, and manufacturing.
Air compressors improve performance, energy efficiency, and environmental impact as technology advances. Here we will discuss the CFM air compressor and how to set them.
What Is 15 CFM At 90 PSI?
CFM stands for Cubic Feet per Minute, which measures the amount of air a compressor can deliver per minute. PSI stands for Pounds per Square Inch, the unit of measure for pressure. When an air compressor is rated at 15 CFM at 90 PSI, it means that the compressor can deliver 15 cubic feet of air per minute when it is operating at a pressure of 90 pounds per square inch.
This measurement is important because it tells you how much air you can expect to be delivered by the compressor under specific conditions. In practical terms, a compressor that can deliver 15 CFM at 90 PSI is a good choice for applications that require a lot of air, such as sandblasting, spray painting, or running air-powered tools like impact wrenches or grinders.
However, it is important to note that the actual performance of a compressor may vary depending on factors such as the type of tool being used, the length of the air hose, and the ambient temperature and humidity.
Types Of Air Compressors: Piston, Rotary Screw, And Centrifugal
Each type of air compressor has advantages and applications, so choosing the right one depends on the specific requirements and usage scenarios. Here are the three main types of air compressors:
- Piston Air Compressor: Also known as reciprocating air compressors, these machines use pistons and cylinder arrangements to compress air. The piston moves up and down, creating a vacuum that draws in air, which is then compressed and stored in a tank.
- Rotary Screw Air Compressor: Rotary screw compressors use two interlocking helical screws to compress air. As the screws rotate, the air volume is reduced, resulting in compressed air. These compressors are more suitable for continuous and heavy-duty industrial applications due to their higher output capacity and efficiency.
- Centrifugal Air Compressor: Centrifugal compressors use a rotating impeller to accelerate air and convert kinetic energy into pressure. They are ideal for large industrial operations requiring high volumes of compressed air. Centrifugal compressors are often used in power plants, chemical industries, and other large-scale applications.
How To Set Up An Air Compressor 15 Cfm At 90 Psi
An air compressor is essential for many applications, from powering pneumatic tools to inflating tires. When choosing the right air compressor, one important factor is the air volume it can deliver. The 15 cfm at 90 psi rating measures the compressor’s ability to deliver air at a specific pressure and flow rate, which is important for ensuring that the compressor can handle the demands of your job.
At 15 cfm, this compressor can deliver a high volume of air, which is ideal for applications that require a lot of air, such as sandblasting, painting, and powering large pneumatic tools. The 90 psi rating is also important, as many tools and applications require a specific pressure to operate effectively.
By providing a steady stream of air at the right pressure and volume, this compressor can help you complete your work more efficiently and effectively. Here are some tips on How to set up an Air compressor 15 cfm at 90 psi.
Choosing A Suitable Location For Your Air Compressor
Selecting the right location for your air compressor is crucial for its optimal performance and longevity. Look for a well-ventilated area to prevent overheating and ensure adequate air circulation. Avoid placing it near corrosive materials or moisture sources to prevent damage.
A flat and stable surface is essential to minimize vibration and noise. Consider the noise level of the compressor when choosing its location to avoid disturbances. A clean and organized space will also make maintenance and access more convenient. Carefully assessing the location will lead to a safer and more efficient air compressor setup.
Preparing The Surface Where The Air Compressor Will Be Placed
Preparing the surface before installing your air compressor is essential for a stable and safe setup. Clean the surface thoroughly to remove any debris, dust, or obstacles. A flat surface is ideal to ensure the compressor remains steady during operation. Consider using rubber or vibration-absorbing pads to minimize noise and vibrations if the floor is uneven.
These pads also prevent the compressor from moving or shifting during use. By preparing the surface properly, you create a solid foundation for the air compressor, reducing the risk of accidents and enhancing its overall performance.
Unpack And Assemble The Air Compressor Components
Assembling your air compressor correctly is crucial for its functionality and safety. Begin by carefully unpacking all the components and ensuring you have all the necessary parts. Follow the manufacturer’s instructions step-by-step to assemble the compressor. Use the provided tools if needed and pay close attention to safety guidelines.
Improper assembly may result in malfunction or even hazardous situations. By taking the time to unpack and assemble the air compressor components correctly, you set the stage for a reliable and long-lasting compressed air system.
Install The Pressure Switch And Regulator
The pressure switch and regulator are vital components for controlling the output of your air compressor. The pressure switch automatically shuts off the compressor when it reaches the desired pressure level and restarts it when it drops. The regulator lets you adjust the output pressure to suit your tools or equipment requirements.
To install these components, refer to the manufacturer’s instructions and ensure they are securely mounted. Properly functioning pressure control enhances the efficiency and safety of your air compressor system.
Connect The Air Compressor To The Power Source
Connecting your air compressor to a suitable power source is crucial to ensure it operates reliably and safely. Before plugging in the compressor, ensure the power source can handle its electrical requirements, including voltage and amperage.
It is recommended to plug the compressor directly into a grounded outlet rather than using extension cords. If an extension cord is necessary, use one with an adequate gauge to prevent voltage drop and overheating. Proper power connection reduces the risk of electrical issues and allows your air compressor to function optimally.
Install The Air Filter And Lubricator
Installing an air filter and lubricator is essential for maintaining the compressed air quality and ensuring the smooth operation of the compressor’s moving parts. The air filter removes contaminants such as dust, oil, and water from the compressed air, preventing damage to pneumatic tools and equipment.
The lubricator supplies controlled amounts of oil to the compressor’s moving components, reducing friction and wear. Follow the manufacturer’s instructions to install these components properly, and make sure to replace filter elements and add lubricant regularly for optimal performance.
Connect The Air Hose To The Air Compressor
You’ll need to connect the air hose to the air compressor to utilize the compressed air. Ensure the air compressor is turned off before proceeding. Attach one end of the air hose to the compressor’s outlet, securing it tightly to prevent leaks.
The other end of the hose can be connected to pneumatic tools or equipment using appropriate fittings. Check for compatibility between the hose and tools to ensure safe and efficient operation. Properly connecting the air hose enables you to utilize the compressed air for various applications.
Check The Oil Level And Add Oil If Necessary
Regularly checking the oil level in your air compressor is vital for its proper functioning and longevity. Consult the manufacturer’s guidelines to locate the oil fill port and dipstick. Check the oil level and ensure it falls within the recommended range.
If the oil level is low, add the appropriate type and quantity specified by the manufacturer. As per the maintenance schedule, regular oil checks and changes will help keep the compressor running smoothly and extend its lifespan.
Turn On The Air Compressor And Let It Run For A Few Minutes
After completing all the necessary setup steps, it’s time to turn on the air compressor and let it run for a few minutes. Before doing so, ensure all connections are secure and there are no signs of leaks. When you power the compressor, it will build up pressure in the tank.
Allowing it to run without load for a few minutes helps lubricate the internal components and ensures everything works correctly. This initial run-in period is crucial for ensuring the compressor’s performance and readiness for use.
Adjust The Pressure And Check For Leaks In The System
Once the air compressor has run for a few minutes, adjusting the pressure settings according to your specific requirements is time. Use the regulator to set your tools or equipment’s desired output pressure. It’s essential to verify the accuracy of the pressure using a pressure gauge. Additionally, thoroughly inspect all connections, fittings, and hoses for any signs of leaks.
Conclusion
The air compressor 15 cfm at 90 psi is a powerful tool that can deliver impressive results. Its ability to produce a consistent airflow at high pressure can make it an essential component of many industrial and manufacturing processes. With its impressive performance, this compressor can help equipment run more efficiently, saving time and money.
The success of this compressor lies in its ability to maintain a steady stream of compressed air, even under high demand. Its specific design and capabilities make it a reliable option for those looking to improve their productivity and meet their compressed air needs. This compressor, 15 cfm at 90 psi, is a valuable investment that can significantly benefit a range of industries and applications.
Faq’s
[rank_math_rich_snippet id=”s-f3756e76-2256-44e8-b55b-0824aa640999″]
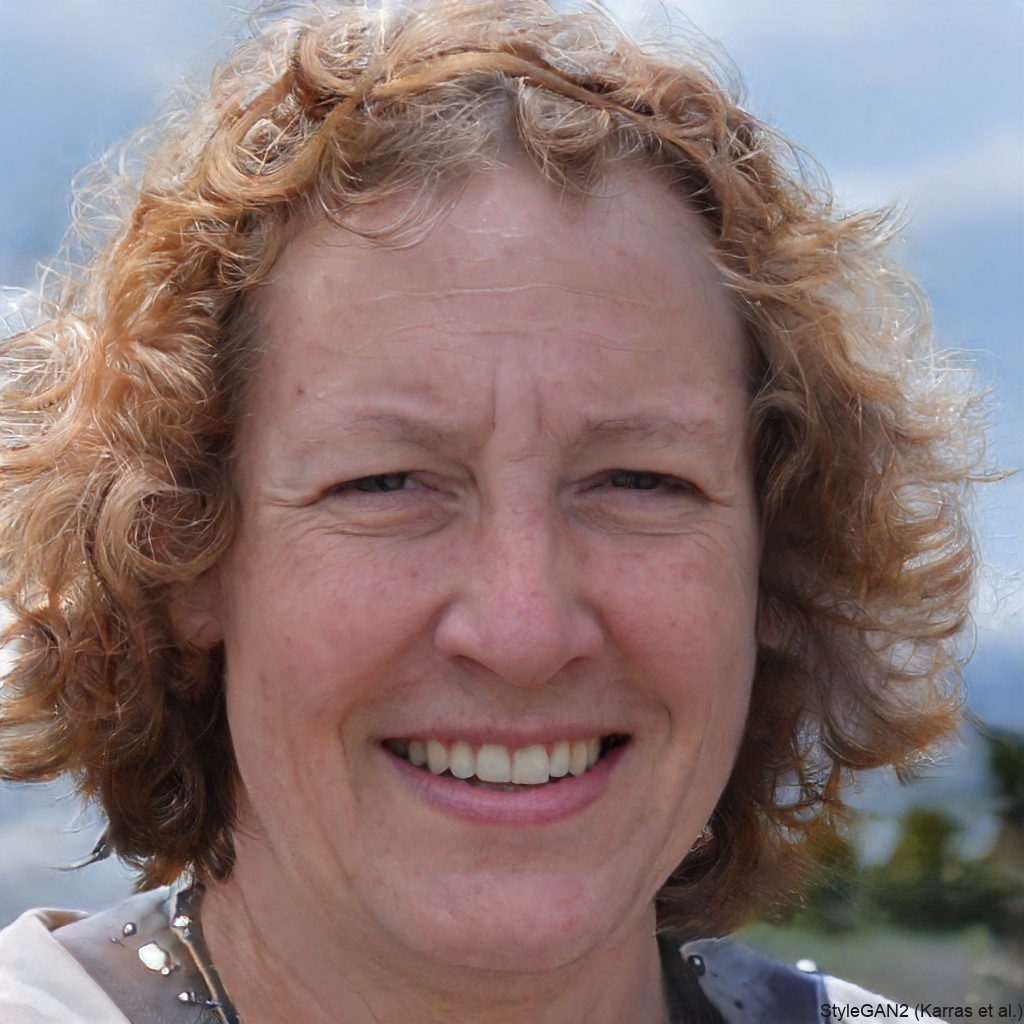
I am passionate about home engineering. I specialize in designing, installing, and maintaining heating, ventilation, and air conditioning systems. My goal is to help people stay comfortable in their homes all year long.