People use air compressors in various industrial and residential settings as versatile equipment. Compressors have many applications, from powering pneumatic tools to inflating tires.
As an important tool for any workshop and manufacturing facility, air compressors are handy for powering various tools and equipment. However, air compressor leaks are a common problem affecting equipment efficiency and performance. One of the most common issues that air compressors face is leaking air, which can cause a significant drop in performance and efficiency.
As a professional, it is crucial to address this. Diagnosing air compressor leaks as soon as possible is important to prevent further damage and keep the equipment working optimally. We will discuss diagnosing and repairing the air compressor leaking air. We understand that identifying the source of a leak can be challenging for many people, but our guide will simplify the process for you. So read on to find out.
What Are The Signs Of An Air Compressor Leak?
Air compressors are essential in many industries, including automotive repair, construction, and painting. However, like any other machine, air compressors can develop problems over time, and one of the most common issues is air compressor leaks. If you suspect your air compressor is leaking, there are several signs to look out for.
Firstly, if you notice a decrease in the air pressure from your compressor, it is a clear sign of a leak. The air compressor is designed to maintain a specific pressure level, and a leak will cause the pressure to drop, resulting in less effective performance. Secondly, if you hear a hissing or whistling sound from the compressor, it is also a sign of an air leak. The air escaping from the system causes the sound.
- Reduced Air Pressure: Reducing air pressure in a confined space can help to prevent the spread of airborne contaminants. This can do using a vacuum cleaner, door opening, or fan.
- Lost Compressor Power: Lost Compressor Power is a meme that refers to a situation where a compressor stops working, and the audio or video is distorted or distorted. People commonly use it as a punchline to express frustration or dissatisfaction with a situation.
Causes And Fixes To Your Air Compressor Leaking Air
Air compressors are an essential tool for many industries, with applications ranging from powering machinery to inflating tires. However, one common issue that can arise with air compressors is leakage. While some may view an air compressor leak as a minor inconvenience, it is a serious issue that can have significant consequences if left unchecked. Here are the Causes and Solutions for Air compressor leaking air.
1. Loose Fittings
Air compressors are widely handy in various industries for powering tools and equipment. However, one common issue that users encounter is when an air compressor starts leaking air. This problem has several causes, but one of the most common is loose fittings. When you don’t tighten fittings securely, they may become loose over time, allowing air to escape. This can cause a decrease in air pressure and affect the compressor’s performance.
Thankfully, there are solutions to this problem. Check all fittings and connections to ensure you properly tighten them as the first step. You should tighten any loose fittings immediately. In some cases, replacing faulty or worn-out fittings with new ones may be necessary. Another solution is to use thread sealant on fittings to prevent future leaks.
2. Damaged Hose
An air compressor is a crucial tool for many industrial and DIY projects. However, it can be frustrating to find that you have a leaking air compressor. The most common cause of air compressor leaks is a damaged hose. The hose is the part of the compressor that carries the compressed air from the compressor to the tool or equipment. A damaged hose can leak air, affecting the compressor’s efficiency and posing a safety hazard.
There are several causes of a damaged hose. One of the most common is wear and tear due to age or frequent use. Exposure to extreme temperatures or chemicals can also damage the hose. In some cases, incorrect hose installation may lead to damage over time. Fortunately, there are solutions to this problem. The first step is to identify the damaged hose and replace it. Choosing a high-quality hose compatible with your compressor and the tools you use is important.
3. Cracked Valve Plate
An air compressor leaking air can be a frustrating problem, but the good news is that it’s usually fixable. One common cause of air compressor leaks is a cracked valve plate. The valve plate is an essential compressor part that helps regulate airflow.
When it becomes cracked, it can cause air to leak out. One solution to this problem is to replace the valve plate. A professional mechanic or an experienced DIYer with the right tools and know-how can do this. Another solution is to try and repair the crack using epoxy or other adhesives. However, this may only be a temporary fix. It’s essential to address the issue quickly before it causes further damage to the compressor or creates a safety hazard.
4. Leaky Piston Rings
Air compressors are essential in many industries, but they can be a headache when they leak air. There are several reasons why air compressors may start to leak air, and one of the common causes is leaky piston rings. Piston rings create a seal between the piston and the cylinder wall, ensuring that compressed air does not escape. However, when the piston rings become worn or damaged, they can no longer create an airtight seal, and air leaks out of the compressor.
There are several solutions to this problem. One solution is to replace the piston rings. This may be challenging, as it requires disassembling the compressor, but it is an effective solution. Another solution is to use a piston ring repair kit. This kit contains materials that can help restore the piston rings’ sealing ability, saving you the cost of replacing them.
5. Faulty Pressure Switch
An air compressor helps get things done quickly and efficiently, making it a valuable tool. However, it can be frustrating when it starts leaking air. There could be several causes for air compressor leaks, but one common reason is a faulty pressure switch. Pressure switches turn the compressor on and off to maintain the tank’s desired air pressure. When the switch malfunctions, it can cause the compressor to run continuously, leading to an air leak.
Thankfully, there are solutions to this problem. The first step is to check the pressure switch for any visible damage or signs of wear. If the switch is damaged, it may need to be replaced. If it looks fine, the issue may be with the internal components.
How To Prevent A Leak
Preventing an air compressor from leaking air is crucial for maintaining its efficiency and prolonging its lifespan. Here are some steps you can take to prevent a leak:
- Regularly inspect the fittings and connections: Check all the fittings, hoses, and connections for any signs of wear or damage. Tighten any loose connections and replace any damaged parts immediately.
- Use thread sealant: Apply thread sealant tape or pipe dope on the threaded connections to create a tight seal. This will help prevent air from escaping through the threads.
- Maintain proper oil levels: If your air compressor is lubricated with oil, make sure to regularly check and maintain the proper oil levels. Low oil levels can cause leaks and reduce the overall performance of the compressor.
- Replace worn-out seals and gaskets: Over time, seals and gaskets can deteriorate, leading to leaks. Inspect them regularly and replace any that show signs of wear or damage.
- Keep the compressor clean: Dirt, dust, and debris can accumulate on the compressor’s components, causing leaks. Regularly clean the compr
Conclusion
An air compressor is a mechanical device that is designed to convert power from an electric motor or a gasoline engine into potential energy that is stored in compressed air. The compressed air can power various tools and equipment, such as pneumatic drills, sanders, and spray guns. Air compressors are widely handy in various industries, including automotive, construction, and manufacturing. Air compressor leaking air can be a frustrating and potentially dangerous issue.
It is important to identify the source of the leak and address it promptly to prevent any further damage or safety concerns. Whether it is a simple fix such as replacing a faulty valve or a more complex issue with the compressor itself, seeking the help of a professional can save time and money and ensure your air compressor’s safe and efficient operation. Regular maintenance and inspection can also prevent future leaks and extend the lifespan of your equipment.
FAQs
[rank_math_rich_snippet id=”s-ef303c5b-a73d-40ea-8d55-51f6430efb4d”]
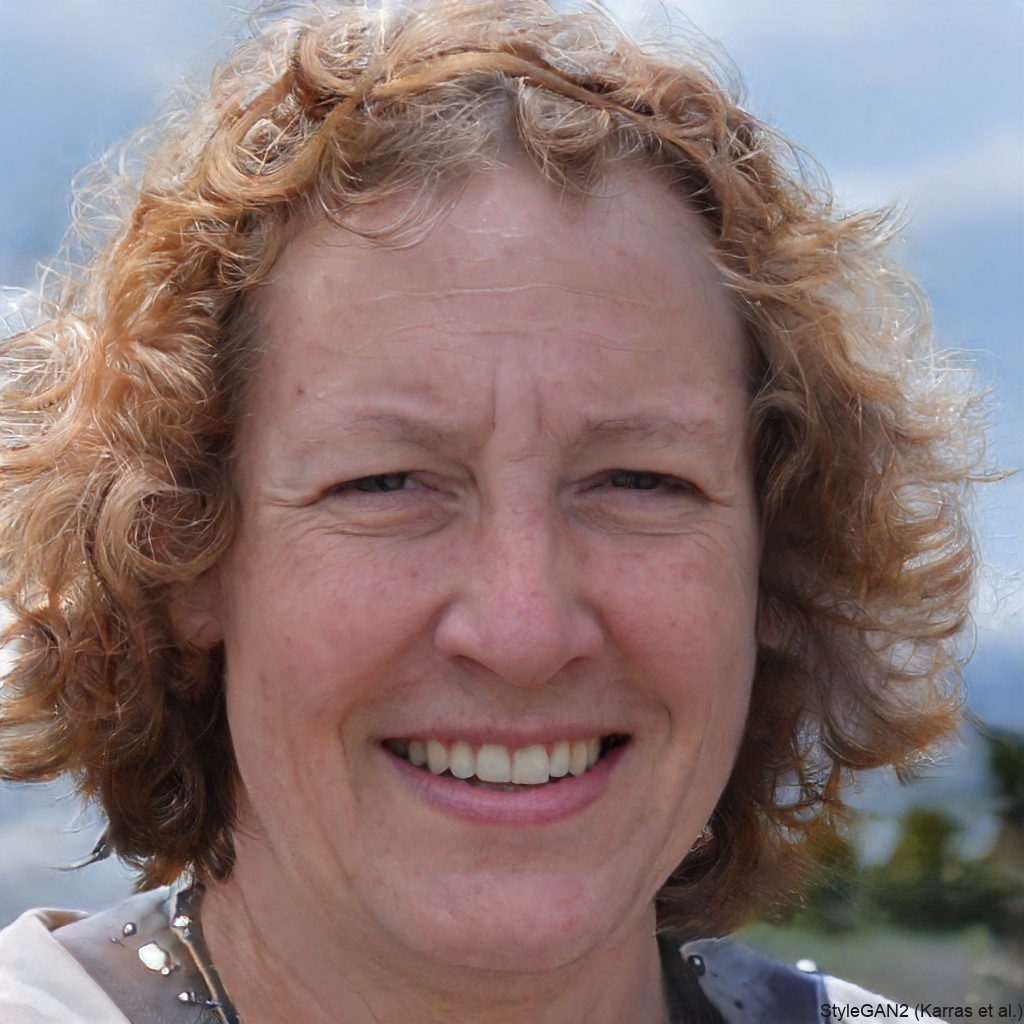
I am passionate about home engineering. I specialize in designing, installing, and maintaining heating, ventilation, and air conditioning systems. My goal is to help people stay comfortable in their homes all year long.