If you’re in the market for an air compressor motor pulley, you may feel a bit overwhelmed by the variety of available options. Not only do you need to consider the size and shape of the pulley, but also its materials, durability, and compatibility with your existing compressor setup.
But fear not – with the right guidance, you can make an informed decision to keep your air compressor running smoothly for years. We’ll cover everything you need to know about air compressor motor pulleys. Also, We’ll provide tips on choosing the correct size and shape of the pulley and offer advice on ensuring that your pulley is compatible with your compressor’s motor.
How To Install A New Air Compressor Motor Pulley?
Installing a new pulley on your air compressor motor is a relatively simple process that can done with just a few tools. Following these steps, you can easily install a new pulley on your air compressor motor, ensuring smooth operation and performance.
However, if you are unsure about any part of the process or do not have experience working with motors, it is always best to consult a professional for assistance. Here are the steps to follow install a new air compressor motor pulley:
- Start by disconnecting the power supply to your air compressor to ensure safety.
- Locate the existing pulley on the motor shaft and remove any set screws or bolts securing it in place.
- Use a pulley puller tool to remove the old pulley from the motor shaft. This tool will help you safely apply pressure and remove the pulley without damaging the motor.
- inspect the motor shaft for any damage or debris once the old pulley is removed. Clean it if necessary.
- Reign your new pulley with the motor shaft, ensuring it fits snugly.
- Secure the new pulley onto the motor shaft using set screws or bolts, making sure they are tightened properly.
- Double-check that the pulley is aligned correctly and spins freely without obstructions.
- Finally, reattach any belts or other components that were disconnected during the process.
The Role Of Pulleys In Air Compressors
Pulleys play a crucial role in the operation of air compressors. They are responsible for transferring power from the motor to the compressor pump, allowing the compressor to compress air and store it for later use. By using a series of belts and pulleys, the compressor is able to operate efficiently and with minimal energy loss.
The pulleys typically come from durable materials such as steel or aluminium and come in various sizes and shapes depending on the specific compressor unit. In addition to their functional role in the operation of the compressor, pulleys also serve as a key component in the compressor’s overall design and construction.
They are often visibly featured on the exterior of the compressor unit and can add to its aesthetic appeal. Proper maintenance and replacement of pulleys are important for the longevity and performance of an air compressor. Regular inspections and adjustments can help ensure that the pulleys are functioning properly and not causing unnecessary wear on other compressor parts.
The Importance Of Properly Sizing Air Compressor Pulleys
The proper sizing of air compressor pulleys is crucial to the efficient operation of the compressor. Pulleys are used to transfer power from the motor to the compressor pump, and if they are not sized correctly, it can lead to various problems. A pulley that is too small will cause the pump to run too fast, which can lead to excessive wear and tear on the compressor components.
Furthermore, it can cause the compressor to overheat and reduce the machine’s lifespan. On the other hand, a pulley that is too large will cause the pump to run too slowly, resulting in insufficient pressure and decreased efficiency.
Additionally, a poorly sized pulley can increase energy costs, as the compressor must work harder to produce the necessary pressure. Therefore, it is important to properly size the air compressor pulleys to ensure that the compressor operates at maximum efficiency.
Consequences Of Incorrectly Sized Pulleys
The consequences of incorrectly sized pulleys can be significant and can negatively impact a system’s performance and efficiency. If the pulleys are too small, they can cause excessive wear on the belt or chain, leading to premature failure.
On the other hand, if the pulleys are too large, they can reduce system speed and decrease torque, leading to decreased efficiency. In addition to these mechanical issues, safety concerns can be associated with incorrectly sized pulleys. For example, if a pulley is too small, there is a risk of the belt slipping off during operation, potentially causing injury or damage to the equipment.
Similarly, if a pulley is too large, it can create excessive tension in the belt or chain, leading to failure or other issues. Therefore, it is important to carefully consider the size and configuration of pulleys when designing or modifying a system and to ensure they are properly installed and maintained to prevent any negative consequences.
Measuring The Diameter Of The Pulley
Measuring the diameter of the pulley is a crucial step in ensuring it functions properly. The diameter of the pulley determines how quickly the belt or cable attached to it moves, affecting the speed and efficiency of the machine that it is a part of.
To measure the diameter of the pulley accurately, it is important to use the right tools and techniques. One of the most common methods is to use a calliper or micrometre, which allows for precise measurements. Another approach is to use a measuring tape or ruler, but this can be less accurate due to potential variations in the shape and curvature of the pulley.
In addition to measuring the diameter, it is important to check for any signs of wear or damage, such as cracks, chips, or unevenness. These issues can impact the performance of the pulley and should be addressed promptly to prevent further damage or potential safety hazards.
How Pulley Ratio Affects Compressor Performance?
The pulley ratio plays a crucial role in determining the performance of your air compressor. It directly influences the speed at which the compressor operates and the amount of air it can deliver. Understanding how the pulley ratio affects compressor performance is essential for optimizing efficiency.
The pulley ratio refers to the relationship between the size of the driver pulley (connected to the motor shaft) and the driven pulley (connected to the compressor pump). By adjusting these sizes, you can control the compressor’s speed.
A larger driver pulley and a smaller driven pulley will result in a lower pulley ratio. This means that the compressor will operate at a slower speed, which can be beneficial in certain scenarios. A lower pulley ratio reduces the wear and tear on the compressor components, resulting in decreased noise levels and increased equipment longevity.
On the other hand, a smaller driver pulley and a larger driven pulley will result in a higher pulley ratio. This increases the compressor’s speed, leading to higher air delivery rates. This is especially useful when you need quick, efficient air compression for large-scale applications.
Troubleshooting Common Pulley Problems
Regarding air compressor-motor pulleys, a few common problems can arise. One of the most important steps in troubleshooting these issues is double-checking that the pulley is aligned correctly and spins freely without obstructions. This ensures that the power from the motor is effectively transferred to the compressor pump.
If you notice any issues with the pulley, such as misalignment or sticking, it’s crucial to address them promptly. Misaligned pulleys can lead to excessive belt wear and reduced efficiency, while obstructed pulleys can cause damage to both the belt and the motor.
Maintenance Tips For Long-Lasting Pulley Performance
Proper maintenance is crucial for ensuring the long-lasting performance of your air compressor-motor pulley. By following these maintenance tips, you can extend the lifespan of your air compressor-motor pulley and ensure optimal performance for years to come. Here are some tips to help you keep your pulley in top shape:
- Regularly inspect the pulley for any signs of wear or damage. Look for cracks, chips, or excessive wear on the belt groove and pulley surface. If you notice any issues, replace the pulley immediately to prevent further damage.
- Keep the pulley clean and free from debris. Dirt and debris can cause the belt to slip and put unnecessary strain on the pulley. Use a brush or compressed air to regularly remove any dirt or dust buildup.
- Check the alignment of the pulley regularly. A misaligned pulley can cause excessive wear on both the pulley and belt. Use a straightedge or laser alignment tool to align the pulley with other components properly.
- Lubricate the pulley bearings as recommended by the manufacturer. Proper lubrication will reduce friction and ensure the smooth operation of the pulley.
- Monitor the tension of the belt regularly. A loose or overtightened belt can cause premature wear on the pulley and decrease its performance. Adjust the tension according to the manufacturer’s specifications.
Conclusion
The proper sizing and installation of air compressor-motor pulleys are crucial for optimal performance and efficiency. Choosing the right size pulleys ensures that the motor operates at the correct speed, preventing strain and potential damage. Additionally, maintaining and troubleshooting pulley issues is essential for long-lasting performance.
Regular inspection, cleaning, and lubrication will help extend the lifespan of the pulley and prevent problems. Following these tips and guidelines ensures that your air compressor motor pulley functions effectively and reliably. Remember, a well-maintained pulley system is key to your air compressor’s overall performance and longevity.
Frequently Asked Questions
[rank_math_rich_snippet id=”s-5773b4a9-2eaa-4063-8051-b40c80bcc79d”]
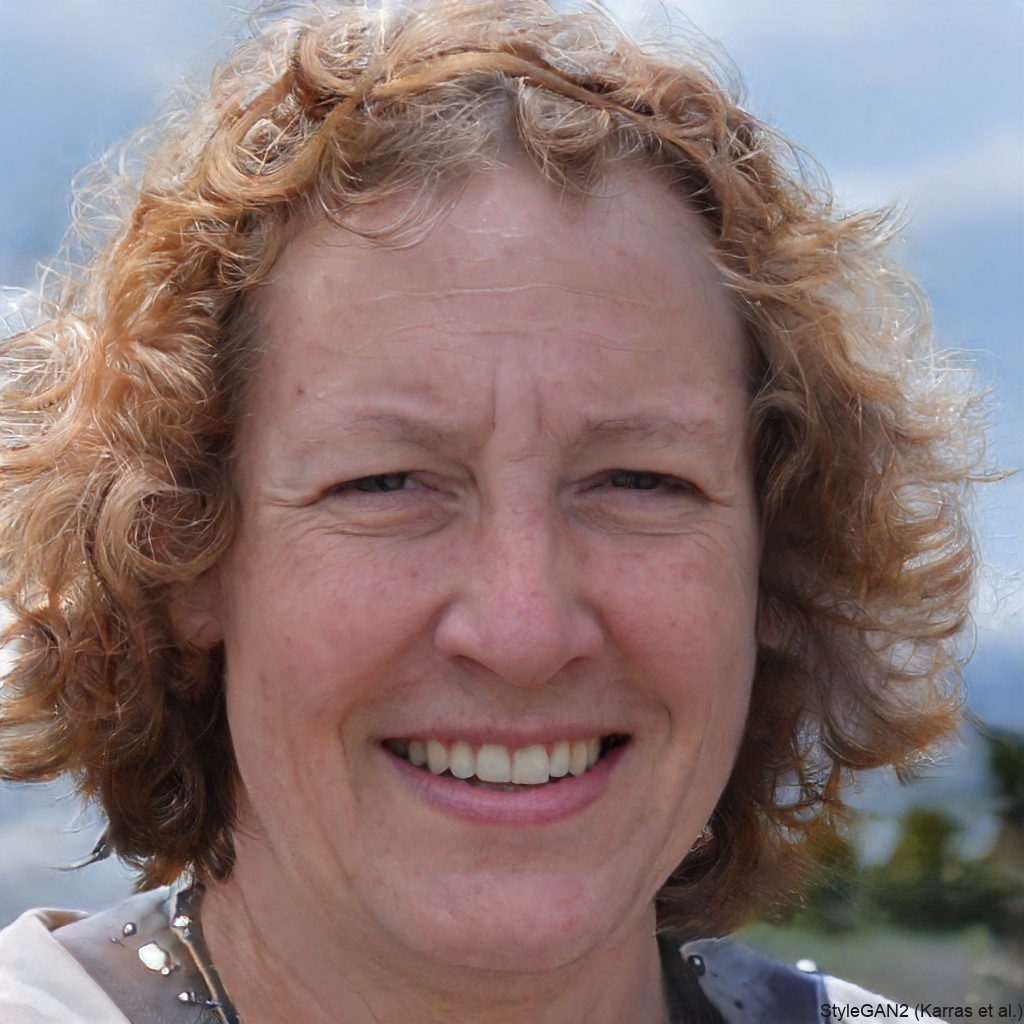
I am passionate about home engineering. I specialize in designing, installing, and maintaining heating, ventilation, and air conditioning systems. My goal is to help people stay comfortable in their homes all year long.