Using an air compressor to power a drill is a simple process that can save you time and effort on your DIY projects. An air compressor works by converting power into potential energy stored in pressurized air, which can then be used to power tools like drills.
You can easily take on your next project using your trusty air compressor and drill combo. However, with the right equipment and some know-how, you can easily use an air compressor to power a drill and complete your DIY projects more efficiently.
Here we will discuss everything you need to know about how to use an air compressor to power a drill from choosing the right equipment, maintaining your air compressor, troubleshooting common issues, and exploring different types of drills that can be used with an air compressor.
How To Use An Air Compressor To Power A Drill: 6 Steps
If you’re looking to use an air compressor to power a drill, there are six simple steps you can follow to get the job done. Remember to use caution when operating this powerful tool and always prioritize safety. Using an air compressor to power a drill can be a great way to get more power and torque than you would from a traditional electric drill.
By following these steps, you can easily use an air compressor to power a drill for all your DIY needs. Just be sure to take safety precautions and wear appropriate protective gear while working with power tools. Here are some steps to guide you on how to use an air compressor to power a drill:
- Make sure your air compressor is compatible with your drill.
- Attach the air hose to the compressor and adjust the pressure.
- Connect the other end of the air hose to the drill.
- Turn on the compressor and allow it to build up pressure.
- Test the drill by squeezing the trigger and listening for the sound of air flowing through it.
- Adjust the pressure and try again until you find the right setting for your project.
Equipment Needed For Air Compressor Drilling
Having the right equipment is crucial when drilling with an air compressor-powered tool like a drill or impact wrench. Using an appropriate hose and fittings that match the size of your air compressor and power tool is vital for optimal airflow and performance.
It’s also necessary to have a pressure regulator knob that controls the compressed air’s flow into the device so that you can adjust the psi output accordingly. Regular compressor maintenance will keep moisture out of your compact air system and prevent rust from forming inside your tank or piston. Don’t forget to wear appropriate safety gear when working with these high-powered tools.
Choosing The Right Air Compressor For Drilling
Choosing the right equipment is critical to successfully use a power tool like a drill with an air compressor. Consider factors such as CFM and PSI ratings when selecting an appropriate compressor. CFM determines how much airflow is necessary to power your tool effectively, while PSI determines smooth operation.
Choose a compressor that meets or exceeds these ratings and perform regular maintenance to ensure optimal performance. Don’t neglect proper airflow, drainage, or rust prevention techniques.
PSI Is Needed For Drilling With An Air Compressor
Proper PSI is crucial when drilling with an air compressor. Depending on the material and type of drill used, standard exercises require between 70-90 PSI. Higher PSI may be necessary when working with more rigid materials like metal or concrete.
Be sure to choose an air compressor that produces enough pressure for your specific drilling needs – a regulator valve can help keep the stress under control. Avoid starting your DIY project with insufficient compressed air pressure by leaving a comment in the comments section.
How To Connect A Drill To An Air Compressor
Proper equipment is crucial for those looking to connect their drill to an air compressor. Select an appropriate air hose and fittings based on your specific needs. Once you have obtained these items, attach the hose to your air compressor’s outlet valve and connect it firmly to your drill’s air inlet valve.
Make sure that you adjust your air pressure accordingly before starting work. Lastly, always prioritize safety by wearing proper eye and ear protection when operating any power tool or pneumatic device.
Using An Air Compressor To Power A Hammer Drill
When using compressed air to power a hammer drill, always use a pneumatic hammer drill that provides more power than electric drills. It is essential to match the tool’s air pressure requirements with the compressor’s capacity while using the correct hose and connectors for secure connections. Always maintain the air compressor and hammer drill for better performance and longevity.
How To Use A Chisel With An Air Compressor
To effectively use a chisel with an air compressor for carving and shaping wood, select an appropriate bit and adjust the pressure accordingly. Connect the chisel to an air hammer or air chisel, then attach it to the compressor via the correct fittings and hose.
It’s crucial to always wear proper safety gear like eye and ear protection. For optimal performancaintain, both tools are regularly. Don’t forget to check the comments section for additional tips on using a compressed-air-powered tool like a chisel for precision work.
Best Air Compressor Accessories For Drilling
To ensure efficient and safe drilling with an air compressor, it is crucial to have the proper accessories. The best air quick – connectessories for drilling include an air hose, quick-connect fittings, compatible drill bits, and an appropriate lubricant. To prevent overheating and damage to your power tool, adjust the pressure using the pressure regulator knob on the portable air compressors.
Make use of impact wrenches or torque wrenches for precise tightening of fasteners in opposite direction positions without any hassle. Regularly maintain the piston by draining moisture through the drain valve and grease gun application to reduce rust buildup.
A larger gallon capacity air tank will provide a better supply of compressed air when using pneumatic tools such as chisels or sanders at higher CFM ratings like orbital sanders or paint sprayers.
Tips For Maintaining An Air Compressor For Drilling
Maintaining an air compressor for drilling involves regular checks of oil level and filter cleanliness to prevent damage or clogs in the line. Using a pressure regulator knob can help achieve precision while reducing unwanted breaks or injuries. Ensure the drill bit is securely attached before using air-powered tools to avoid wobbling or breakage. Lastly, always wear suitable safety gear when operating pneumatic tools.
What Types Of Drills Can You Use With An Air Compressor?
If you’re looking to use an air compressor to power a drill, it’s important to choose the right type of drill for the job. Most types of drills can be used with an air compressor, including electric and pneumatic drills. However, it’s important to note that not all drills are created equal when using them with an air compressor.
For example, a hammer drill may not work as well with an air compressor as a standard rotary drill. It’s also important to make sure that your drill is compatible with the size and pressure output of your specific air compressor. With the right combination of drill and air compressor, you can achieve powerful and efficient drilling performance for all your DIY projects.
How To Use An Air Compressor With A Cordless Drill
Using an air compressor with a cordless drill requires a little effort but is easy to do with proper planning. Selecting the right pneumatic tool, such as an impact wrench, is crucial for smooth and efficient drilling without compromising safety guidelines. Additionally, it is essential to check if your portable air compressors have the right CFM rating, and the best way to achieve this is by adjusting its pressure regulator knob.
Using A Torque Wrench With An Air Compressor
When using a torque wrench with an air compressor, it is essential to follow specific guidelines. To begin with, check if your drill is compatible with your compressor’s air pressure and volume. Some drills may require additional adapters or accessories for this purpose.
Additionally, it is crucial to abide by your manufacturer’s instructions and safety guidelines while utilizing an air compressor to power your drill. Lastly, ensure that you check the torque specifications of fasteners before adjusting the torque wrench accurately for precise results.
How To Sand With An Air Compressor And Sander
Select the appropriate grit sandpaper for your project to achieve precision while sanding with an air compressor and sander. Reduce airborne particles by using a dust collection system and protect yourself from harmful dust by wearing protective gear.
For surfaces that are angled or contoured, consider using a smaller sanding pad attachment. Regularly drain the moisture from your air compressor tank and adjust the airflow and pressure regulator knob as needed. After each use, clean your sander with compressed air to optimize its performance.
Using Grease Guns With An Air Compressor
Lubricating various machinery parts can be effortless with a grease gun powered by an air compressor. But before you start greasing your equipment, make sure that the grease gun is compatible with your portable or piston-driven air compressor.
Attach a hose to your grease gun and connect it carefully to your compressor’s fitting. Fine-tune your setup by adjusting airflow and pressure regulator knobs. Finally insert nozzle of grease gun into fittings and use it in the opposite direction for precision greasing.
How To Troubleshoot Common Issues When Drilling With An Air Compressor
When using an air compressor to power a drill, it is vital to troubleshoot common issues to ensure efficient operations. First, always check the air pressure and inspect the drill bit before drilling. Next, clean the air filter regularly and use the right lubricant for improved precision of your power tool while avoiding rust buildup on its piston or valve.
Don’t forget to check for leaks in your hose or compressed air line that may affect drilling performance negatively when connected to different tools like impact wrenches or torque wrenches. Lastly, make sure you’re using compatible accessories like pneumatic tools such as an air hammer or chisel with your portable air compressors’ gallon size tank and CFM rating.
Air Compressor Not Building Pressure
To troubleshoot an air compressor not building pressure issue, first ensure that the tank drain valve is closed and the intake filter is clean. Then, inspect the compressor’s piston rings and valves for wear or damage. Set the compressor’s regulator to appropriate psi and look for leaks in hoses, connections, or fittings. Remember to maintain your air compressor, including draining water from its tank regularly to prevent rust or moisture buildup.
Troubleshooting Air Leaks In Compressor Lines
When your compressor experiences air leaks in the compressor lines. It can reduce the air pressure and affect the performance of your pneumatic power tools like impact wrenches. Hammers, torques, chisels, and drills. Troubleshooting this problem involves checking for loose fittings or damaged hoses.
While regularly maintaining the compressor to prevent rust and moisture accumulation. Replacing damaged components like valves, hoses, or pistons and tightening all connections using precision fasteners. Or paint sprayers can help seal the system and improve airflow.
What Is The Cost Of Using An Air Compressor For Drilling?
The cost of using an air compressor for drilling varies depending on the compressor size, drill type. And duration of use. While they may require a higher initial investment, air compressors are generally more cost-effective than electric drills . In the long run because they can save money on electricity bills and maintenance costs. Proper usage and regular maintenance can also help reduce costs over time.
Cost Of Air Compressor Maintenance
When using an air compressor for drilling, it’s crucial to keep the overall cost in mind by considering all associated expenses like maintenance and accessories. Preventing air leaks by maintaining the compressor and checking for faulty fittings or hoses is crucial to ensure proper airflow and air pressure for efficient drilling operations.
Troubleshooting air leaks can be challenging; however, replacing damaged components and tightening connections through proper maintenance can help reduce costs and improve performance.
Cost Of Accessories For Drilling With An Air Compressor
Accessories such as drill bits and grease guns are important when using compressed air to power tools like drills. In addition to the size and type of drill bit being used, the impact and torque wrench are commonly used pneumatic tools.
Although there might be a larger upfront investment in purchasing a new compressor compared to electric drills or other power tools, it provides compressed air which is essential for various DIY projects. Efficient usage combined with proper maintenance reduces costs over time by preventing rust buildup on tools or components within the system.
Conclusion
Using an air compressor to power a drill can be a game-changer for DIY enthusiasts. It offers convenience, power, and versatility that traditional drills cannot match. However, it’s essential to understand the equipment required and how to maintain it properly to ensure longevity.
Familiarizing yourself with the various drills and their usage is equally important. Troubleshooting common issues can also save time and money in the long run. All this information is crucial and can be overwhelming at first. To make things easier for you, we have compiled a guide on how to use an air compressor to power a drill that covers everything from choosing the right air compressor to troubleshooting common issues.
Frequently Asked Questions
[rank_math_rich_snippet id=”s-23bf6d8e-7f1c-4352-8d8b-0a2938bbcd2f”]
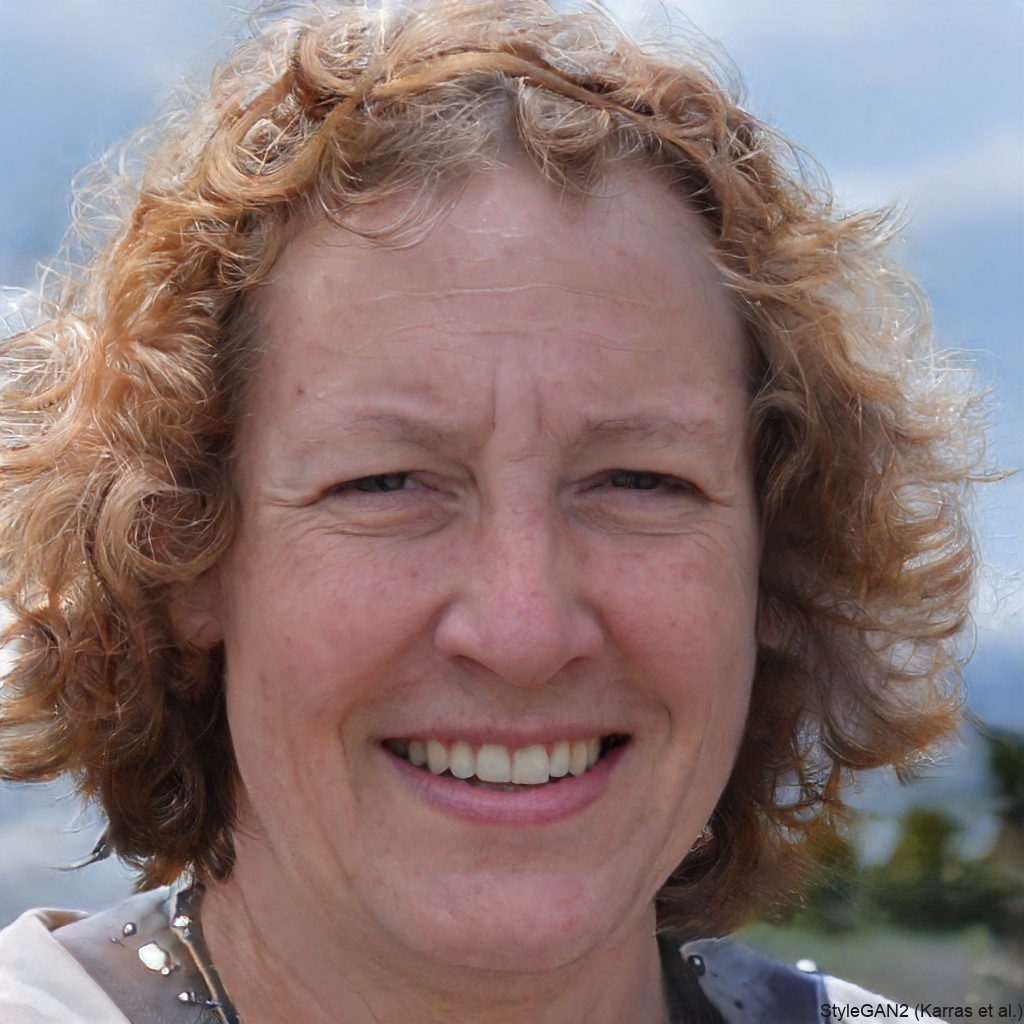
I am passionate about home engineering. I specialize in designing, installing, and maintaining heating, ventilation, and air conditioning systems. My goal is to help people stay comfortable in their homes all year long.