Hydraulic systems are an excellent choice if you’re looking for a powerful and efficient way to move heavy loads or operate machinery. However, they require a power source to work, and that’s where air compressors come in.
You can generate pressurized air that powers a hydraulic cylinder using an air compressor. This combination of technologies is widely handy in various applications, from construction equipment to industrial machines.
Here, we will explore how to use an air compressor to power a hydraulic cylinder. We will cover the basics of how hydraulic systems work, the benefits of air compressors, and the steps involved in setting up and operating this type of system. So, if you are interested in learning how to improve the Performance and efficiency of your hydraulic systems, keep reading.
What Is An Air Compressor?
An air compressor is a machine that converts power, usually from an electric motor or gasoline engine, into potential energy stored in compressed air. Compressed air can be used for various purposes, such as powering pneumatic tools, inflating tires, and cleaning materials.
Air compressors come in different sizes and capacities, ranging from portable models that can be used for small jobs to large industrial models that can supply compressed air to entire factories or manufacturing plants. The essential components of an air compressor include a compressor pump, an electric motor or gas engine, an air tank, and various controls and safety features.
What Is A Hydraulic Cylinder
A hydraulic cylinder is a mechanical device that converts hydraulic energy into linear motion. It consists of a piston, rod, cylinder barrel, and end caps, all working together to produce force in a specific direction.
Hydraulic cylinders are commonly handy in various construction, manufacturing, and transportation applications. These devices are popular for their ability to produce high-force output and precise motion control, making them a popular choice for heavy-duty machinery and equipment. They come in various sizes and designs, allowing them to fit different requirements and specifications.
8 Steps On How To Use An Air Compressor To Power A Hydraulic Cylinder
Hydraulic systems move heavy loads and apply force in manufacturing, construction, and transportation industries. An air compressor can provide the power needed to run these hydraulic systems, making them more efficient and versatile.
Understanding how to use an air compressor to power a hydraulic cylinder is essential. To use an air compressor to power a hydraulic cylinder, follow these step-by-step guidelines:
Ensure Safety Precautions
When using an air compressor to power a hydraulic cylinder, it is essential to ensure that safety precautions are taken to avoid accidents or injuries. Firstly, wearing the appropriate protective gear, such as safety glasses, gloves, and earplugs, is essential to prevent any harm from flying debris, noise, or accidental spills.
Additionally, inspecting the equipment for any damage or leaks before using it and ensuring the system is connected correctly and secured. It is also essential to follow the manufacturer’s instructions and guidelines for using the drill module air compressor oil viscosity and hydraulic cylinder and to avoid exceeding the maximum pressure or load capacity.
1.Connect The Air Compressor
To successfully utilize an air compressor to provide power to a hydraulic cylinder, it is essential to properly connect the air compressor flow rates to the hydraulic system. Ensure that the air compressor and the hydraulic cylinder are in proper working condition and have the necessary safety features.
Identify the appropriate connection points on the air compressor and the hydraulic cylinder. These connection points may include air inlet ports, pressure relief valves, and hydraulic fluid ports. Keep a close eye on the pressure gauge and the Performance of the hydraulic cylinder during operation.
2.Check The Air Compressor Settings
Before starting any task, ensuring your tools function correctly is crucial. One of the most essential tools in any workshop is the air compressor. However, checking the air compressor with hydraulics settings is crucial to guarantee optimal Performance.
These settings can significantly impact the compressor‘s output and efficiency, so it is essential to pay attention to them. The first thing to check is the pressure setting.
The pressure setting should match the task’s requirements and not exceed the maximum limit. To control the air pressure, you should set the air regulator correctly. Another critical setting to check is the compressor‘s oil level.
3.Connect The Hydraulic Cylinder
Connecting the hydraulic cylinder involves joining the cylinder to the hydraulic pump, valves, and other hydraulic components. This connection is crucial to ensure the hydraulic application system operates efficiently and effectively.
Depending on the system’s requirements, the relationship can come using different methods, such as threaded connections, flanges, or welded joints. When connecting the hydraulic cylinder, it is essential to ensure the connection is secure and leak-proof. Any leaks in the system can lead to reduced efficiency and even total system failure.
4.Bleed The Air
Using an air compressor critical to power a hydraulic cylinder is common in many industrial applications. However, trapped air in the hydraulic system can cause issues with the Performance of the cylinder.
Knowing how to bleed the air out of the system is essential to prevent this. Bleeding air involves removing trapped air bubbles and replacing them with hydraulic fluid. The process is relatively straightforward, and you can do it with essential tools.
5.Test The System
An air compressor lubricant can be handy when powering a hydraulic pressure cylinder. However, knowing how to properly test the system to ensure it functions correctly and safely is essential. The step is to check that the air compressor control panel provides enough pressure to power the hydraulic cylinder.
This can be done using a pressure gauge to measure the air pressure at the compressor outlet and compare it to the hydraulic cylinder‘s required pressure.
Finally, the hydraulic cylinder should be appropriately connected to the pump, and any necessary adjustments to the cylinder‘s position, pressure relief valves, or flow control valves should be made.
6.Operate The Hydraulic Cylinder
Before connecting the hydraulic power cylinder to the air compressor head, check the oil level and ensure tight connections. Once you confirm everything is in order, you can connect the hydraulic cylinder to the air compressor.
To operate the hydraulic cylinder, let the air compressor run until it reaches the required pressure. Once the air compressor has achieved the desired pressure, you can activate the hydraulic cylinder by opening the control valve. This will enable the hydraulic fluid to flow into the cylinder and extend the piston, allowing you to move the load.
7.Monitor Performance
When using an air compressor to power a hydraulic cylinder, it is critical to monitor the Performance of your system. A hydraulic cylinder converts hydraulic energy into mechanical energy, and an air compressor fluid provides the necessary power to operate it.
One way to monitor Performance is to monitor the air pressure gauge. Ensure the pressure remains within the recommended range to ensure the cylinder operates appropriately.
You should also check for leaks in the air supply lines or the cylinder. Any leak in the system will cause a pressure drop, which will negatively impact Performance.
8.Shutdown And Maintenance
After completing your task, turn off the air compressor and disconnect the hydraulic cylinder. Follow proper maintenance procedures for the air 2hp compressor and hydraulic cylinder, such as cleaning, lubricating, and storing them in a suitable location.
Remember, following the manufacturer’s instructions and guidelines for your air AC compressor and hydraulic cylinder is vital to ensure safe and efficient operation.
Types Of Hydraulic Cylinder
A hydraulic cylinder is a mechanical device that utilizes the power of hydraulic fluid to generate linear force and motion. It consists of various components, such as a cylindrical barrel, a piston, a piston rod, and seals. The operation of a hydraulic cylinder is based on Pascal’s law, which states that when pressure is applied to a confined fluid, it is transmitted equally in all directions.
- Single-acting hydraulic cylinder
- Double-acting hydraulic cylinder
- Telescopic hydraulic cylinder
- Plunger hydraulic cylinder
- Piston hydraulic cylinder
How To Choose A Hydraulic Actuator
When choosing a hydraulic actuator, there are several factors to consider. Consider the amount of force and the distance the actuator needs to move to select the appropriate size. Consider factors such as temperature, humidity, and corrosive substances to ensure that the actuator is suitable for its exposed conditions. Considering these factors, you can choose a hydraulic actuator best suited for your specific application. Here are some key bullet points to help guide your decision:
- Determine the required force and stroke length:
- Consider the operating environment:
- Evaluate speed and response requirements:
- Assess mounting options:
- Consider maintenance and serviceability:
- Evaluate safety features:
How Does Hydraulic Actuator Work
Hydraulic actuators are a key component of hydraulic systems and are crucial in converting fluid power into mechanical force. The basic principle behind hydraulic actuators is using fluid pressure to move a piston or a rod. When hydraulic fluid is pumped into the cylinder, it creates pressure, which pushes against the piston or rod, causing it to move. This movement can be linear or rotary, depending on the design of the actuator.
By controlling the flow of hydraulic fluid, the operator can control the speed and direction of the actuator’s movement. Hydraulic actuators are widely used in various industries for lifting heavy loads, operating machinery, and control valves. Their efficiency, reliability, and ability to generate high force make them essential in many hydraulic systems.
Conclusion
Knowing how to use an air compressor to power a hydraulic cylinder can be incredibly useful in various applications. Using an air CFM Rotary Screw Air compressor to power a hydraulic cylinder is a simple and efficient method for industrial applications.
By following the straightforward guidelines provided, any individual with basic knowledge of mechanics can operate an air compressor body to control the movement of a hydraulic cylinder. It is essential to ensure the proper selection and sizing of the air compressor efficiency and hydraulic cylinder to achieve optimum performance and avoid potential safety hazards.
With this knowledge, one can confidently and effectively utilize this technique in various industrial settings. Regular maintenance, including checking for leaks, proper lubrication, and monitoring pressure levels, is crucial to ensure safe and efficient operation.
FAQs
[rank_math_rich_snippet id=”s-f7890989-05ec-4c19-bba6-ab4c69cac0d2″]
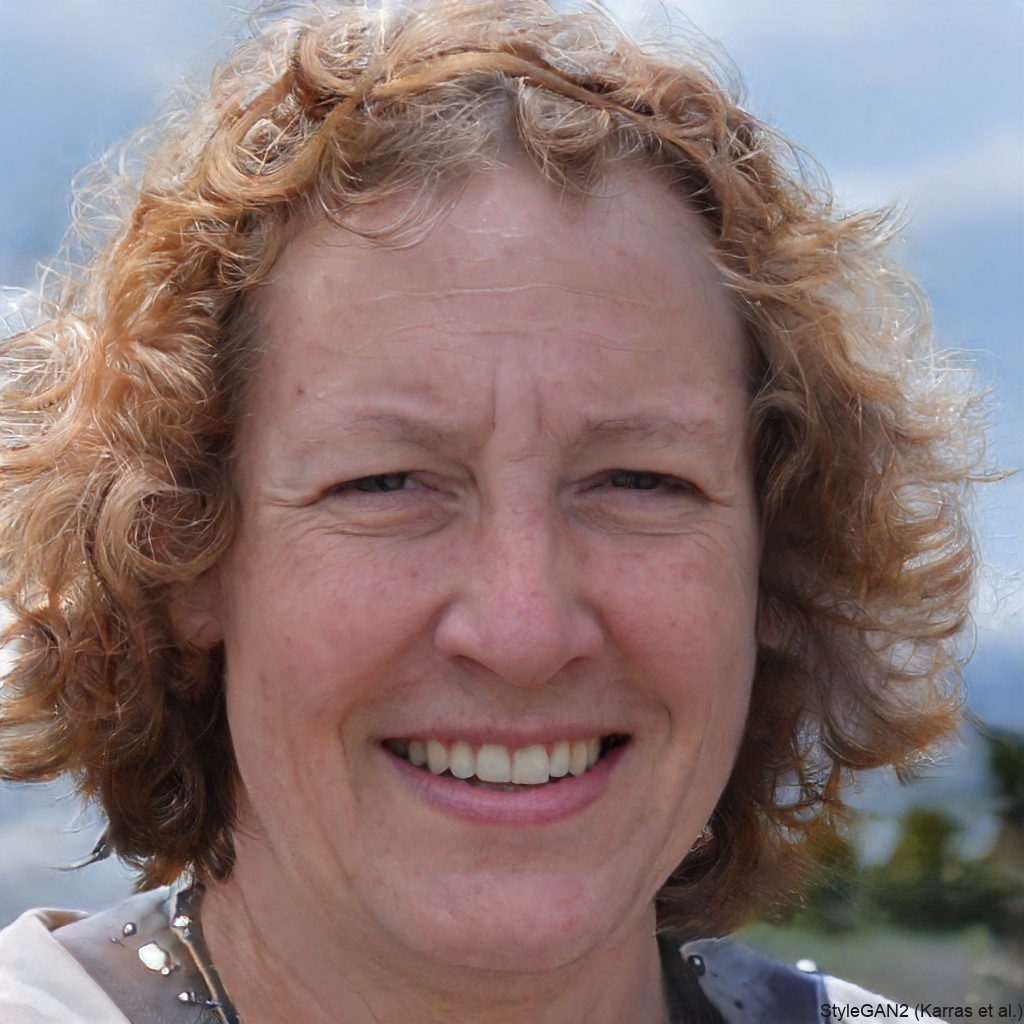
I am passionate about home engineering. I specialize in designing, installing, and maintaining heating, ventilation, and air conditioning systems. My goal is to help people stay comfortable in their homes all year long.