Whether you are a DIY enthusiast or a professional needing heavy-duty equipment, having the right air compressor can make all the difference. This comprehensive user manual will take you through everything you need about rigid air compressors.
We have covered you, from understanding the different types available and choosing the right size for your needs to installation, operation, and troubleshooting. We will also discuss the various applications of air compressors in different industries and provide tips on proper maintenance and care. So whether you are a beginner or an experienced user, this guide is your go-to resource for all things related to air compressors.
How To Use Rigid Air Compressors For Every Need
Using a rigid air compressor is a relatively straightforward process, but it is important to follow the proper steps to ensure safe and effective operation. First, ensure the compressor is properly set up and connected to a power source. Before turning on the compressor, check the oil level and add more if necessary.
Next, adjust the pressure regulator to the desired level for your application. Once everything is set up, turn on the compressor and allow it to build pressure until it reaches the desired level.
To use the compressed air, attach a hose or tool to the outlet valve and release the air by pulling the trigger or engaging the tool. When you finish using the compressor, turn it off and disconnect any hoses or tools. Regular maintenance of your rigid air compressor will help ensure its longevity and optimal performance.
Types Of Rigid Air-Compressors
Rigid -air compressors are a vital component in industrial and manufacturing settings. Several types of rigid air- compressors are available in the market, each with unique features and benefits. The most common types of rigid air- compressors include reciprocating compressors, rotary screw compressors, and centrifugal compressors. They work by using a piston to compress air into a storage tank.
These compressors are ideal for small to medium-sized operations and are relatively inexpensive. Rotary screw compressors, on the other hand, are more efficient and operate at higher capacities than reciprocating compressors.
They use two interlocking screws that rotate together to compress air continuously. These compressors are best suited for large-scale industrial operations that require a constant supply of compressed air.
Choosing The Right Size Air Compressor For Your Needs
Choosing the right size air compressor for your needs is essential to ensure efficient and effective operation. When considering the size, it’s important to evaluate the tasks you’ll be performing and the tools you’ll be using. A small air compressor may suit light-duty tasks like inflating tires or powering a nail gun.
In contrast, a larger compressor may be necessary for heavy-duty jobs like sanding, grinding, or spray painting. One important factor to consider when selecting the right size air compressor is the amount of pressure and volume of air required for your tools. To operate efficiently, many tools need specific pressure and CFM requirements (cubic feet per minute). If the compressor doesn’t deliver enough pressure or volume, the tools won’t work properly, leading to frustration and wasted time.
Installation And Setup Of Rigid Compressors
Rigid compressors are essential for various industrial applications, including automotive repair, construction, and manufacturing. The installation and setup of these compressors require careful planning to ensure optimal performance and safety. The first step is selecting the appropriate model based on the application’s requirements.
Once the compressor has been chosen, it is important to consider the location and placement of the unit. It should be installed in a well-ventilated area, away from heat sources and combustible materials. The next step is to connect the air supply lines and electrical connections. Following the manufacturer’s instructions carefully ensures all connections are tight and secure.
Properly Operate A Rigid-Air Compressor
A rigid-air compressor is essential to ensure it runs effectively and efficiently. Before using a rigid-air compressor, it is crucial to read the manufacturer’s instructions carefully and understand all the safety measures. Inspecting the machine to ensure it is in good working condition and all parts are properly lubricated is also necessary.
When starting the compressor, ensure it is placed flat and securely grounded to avoid electrical hazards. Check the oil level and pressure gauge and adjust them accordingly, if needed. Always wear the appropriate safety gear, including eye and ear protection, when operating a rigid-air compressor.
To use the compressor, connect the air hose to the compressor and the tool, ensuring the connections are tight and secure. Turn on the compressor and allow it to build up pressure before using the tool.
Safety Considerations When Operating Rigid Compressors
To ensure your safety when operating a rigid compressor, always wear the appropriate safety gear, inspect the compressor for damage or leaks, and follow manufacturer instructions for maintenance and lubrication.
Additionally, it is important to keep the work area clean and free from any obstructions that could interfere with safe operation. Avoid operating the compressor in wet or damp conditions, as this can pose a risk of electrical shock. When working with compressed air, always be mindful of the pressure and avoid exceeding the recommended level for your specific tool or application.
Applications Of Rigid-Air Compressors In Various Industries
Rigid- air compressors find applications in construction, automotive, manufacturing, and other industries. They power tools, inflate tires, operate machinery, and provide compressed air for various processes. Optimal performance is achieved by choosing the right size and capacity compressor.
When it comes to using a rigid-air compressor, safety should always be the top priority. Before operating the compressor, inspect the level and pressure gauge and adjust them if needed. It’s crucial to wear the appropriate safety gear, including eye and ear protection, to protect yourself from hazards.
Troubleshooting Common Rigid-Air Compressor Issues
To troubleshoot low pressure, check and clean or replace the air filter and fix any leaks. For overheating, ensure proper ventilation and oil level. Noisy operation requires tightening screws and professional inspection.
Slow pressure build-up may indicate air leaks or pump issues. Uneven pressure can be resolved by inspecting hoses and replacing filters. Difficulty starting may require checking the power supply and starter capacitor for electrical problems.
Maintenance And Care Of Your Rigid-Air Compressor
To keep your Rigid- air compressor in optimal condition, regularly check oil levels, clean or replace the air filter, inspect belts, hoses, and fittings for damage, and keep the compressor clean. Ensure the pressure switch and safety relief valve are functioning properly.
Proper maintenance and care are vital to ensuring the longevity and efficient performance of your Rigid- air compressor. Regularly checking the oil levels is crucial, as low oil can lead to overheating and damage to the compressor’s components. Clean or replace the air filter routinely to prevent dust and debris from clogging the system.
Conclusion
A powerful, rigid air compressor can be used for various applications, from inflating tires to powering air tools and industrial machinery. Whether you’re a DIY enthusiast or a professional needing heavy-duty equipment, a rigid -air compressor is out there to meet your specific needs.
Understanding the different types of compressors available, choosing the right size for your requirements, and following proper installation, operation, and maintenance procedures are crucial for optimal performance and longevity. Safety should always be a top priority when working with air compressors, so follow all safety guidelines and precautions.
Frequently Asked Questions
[rank_math_rich_snippet id=”s-f4206c9a-45e3-4e39-ab20-504dcebd638c”]
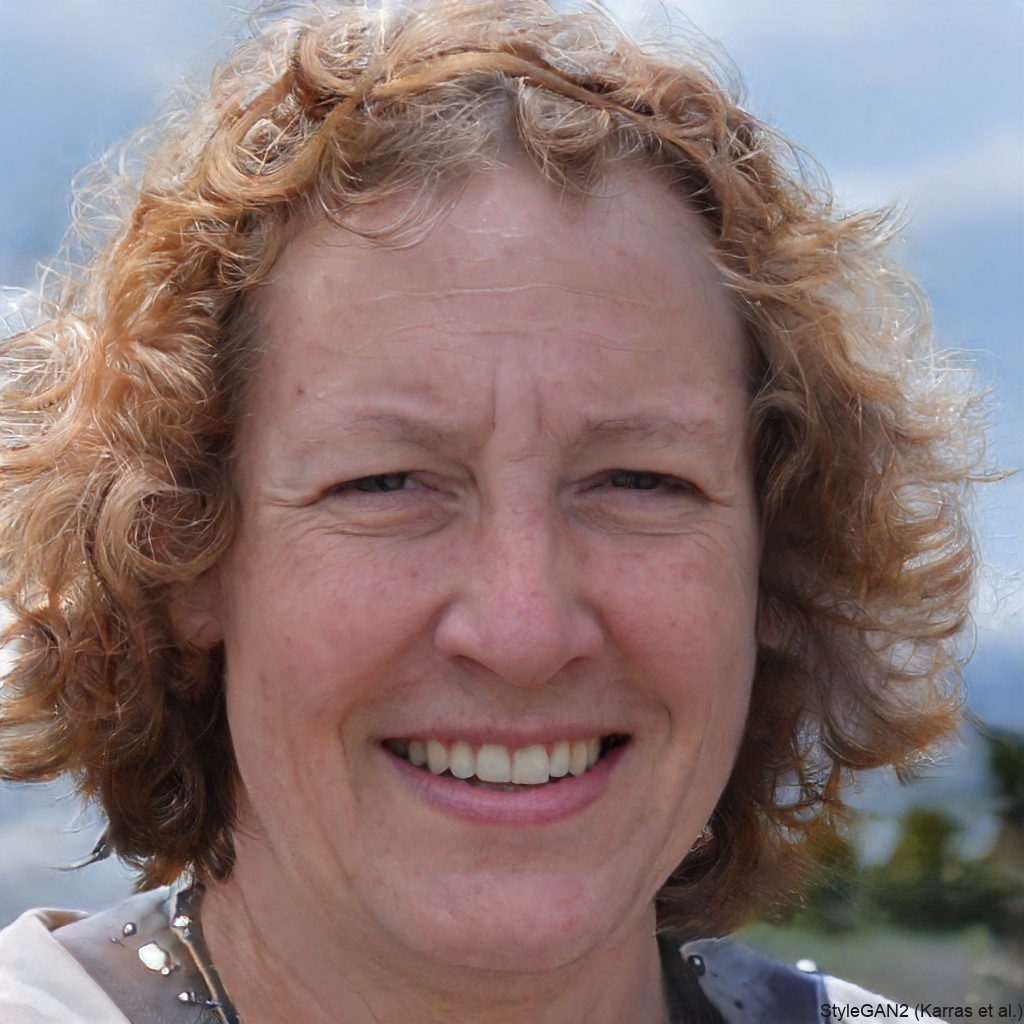
I am passionate about home engineering. I specialize in designing, installing, and maintaining heating, ventilation, and air conditioning systems. My goal is to help people stay comfortable in their homes all year long.