Air compressors are essential in many industries, from construction to manufacturing. They work by compressing air and powering various tools and machines. Have you ever gotten an air compressor delivery and noticed the compressor sitting on the ground without any safety precautions? Your air compressor tank likely has.
While avoiding air compressor tank safety hazards is relatively easy, there are still ways to ensure safety while using compressed air. Here, we will cover air compressor tank safety precautions like powering down fully before repairs, draining the compressor tank often, keeping hands away from compressed air tools, checking the electrical outlet, etc. We hope this will help you understand the risks of compressed air equipment and how to protect yourself.
What Is An Air Compressor Tank?
An air compressor receiver tank is part of a system that holds compressed air until needed. Manufacturers usually make it of mild steel and may prime it to prevent corrosion and increase longevity. Various materials, such as galvanized or epoxy-coated steel, can make the interior of the tank, but speciality applications may require the tank to be made of stainless steel.
Air Compressor Tank Safety Precautions: 10 Tips
Air compressor tank safety precautions include checking the manual with your unit for the maximum recommended speed and ensuring you never run your compressor at speeds exceeding this level. Also, position the safety valves on your air tank to prevent water from collecting inside the unit.
This will help prevent a potential explosion and the risk of injury to the operator. Another safety precaution is placing a filter or screen at the intake valve to keep the air intake clean. This will help to prevent dirt, debris, or other impurities from entering the air system and causing damage to the equipment or surrounding environment. Scroll down for 10 more safety precautions:
1. Power Down Fully Before Repairs
Draining air compressors regularly is a good practice to prevent them from rusting and exploding. Remember to lock out power sources before refilling fuel, oil, water, or DEF. This will help prevent accidental injuries or leaks. Finally, keep hands, fingers, hair, and clothing away from the air compressor due to its rotating parts.
2. Allow Time For The Compressor To Cool Down
Always allow the equipment to cool down before handling it with an air compressor. This will help to prevent burns and other injuries. Air compressor tanks can be dangerous if you touch hot parts, coolants, or lubricants during or shortly after usage.
If you do not wear gloves or take precautions, this can lead to severe burns. Additionally, it is essential to drain the tank regularly to prevent rust and explosions. To avoid injuries, it is important to protect your hands, fingers, hair, and clothing from the rotating parts of the air compressor.
3. Drain The Compressor Tank Often
To prevent explosive decompression and corrosion in compressor tanks, it is essential to drain the tank regularly. We recommend using a pneumatic drain system that automatically detects when the compressor tank is full and shuts down the compressor to avoid overfilling for safety reasons.
Additionally, it is essential to drain the tank when replacing parts or cleaning the equipment. This will help prevent excess condensation from forming and lead to a safer overall operation of the compressor. One should shut down and disconnect air compressors from the power source before draining a tank. This will prevent accidental damage to the compressor during the process.
4. Keep Hands, Fingers, Hair, And Clothing Away
Operators must always remain in control of the compressor unit and stand on a level surface away from the unit. Additionally, operators must wear protective equipment and clothing while operating an air compressor. This includes safety goggles, a high-quality dust mask, and other appropriate safety apparel. Ensuring all hoses are fitted tightly and free of dirt and debris is important to prevent injury.
5. Check The Electrical Outlet
Before plugging in the air compressor, ensure the electrical outlet is properly grounded. This will ensure the air compressor does not overheat or put too much pressure. Additionally, ensure that the outlet is not defective or malfunctioning.
To ensure that you use the correct rating for the outlet, use a voltage tester to test it for the correct voltage. Also, avoid using outlets with missing or broken ground prongs. These safety precautions will help protect yourself and the air compressor from damage.
6. Choose The Right Compressor Location
A safety valve is a vital safety feature on air compressors. It allows compressed air to flow back into the tank when the pressure reaches a preset level. It ensures that compressed air doesn’t enter the system at unsafe pressures and potentially cause damage to the air compressor or the air tank.
In addition, air compressors typically have safety valves to reset high pressure if the system experiences pressure loss automatically. This helps prevent excess compressed air from entering the system, which could result in damage. Additionally, you can use filters and screens to improve air quality and keep the compressed air clean. These safety measures help ensure that air compressors work safely and efficiently while protecting people and property from harm.
7. Do Not Use Pvc Pipe
Using PVC pipes in compressed air applications can be a safety risk. They can easily crack and burst, potentially causing pieces of shrapnel to fly. This can lead to serious injuries. It is also important to use secure, standard fittings for airlines and to label each airline with a tag indicating the maximum working pressure.
Using an OSHA-approved nozzle helps control the airflow better and reduces the risk of injury. These safety precautions help ensure that compressed air systems are safe and effective.
8. Secure Tools And Hoses Before Starting The Compressor
Air compressor safety is vital for the safety of the air compressor and the people using it. Before starting the air compressor, ensure all hose fittings are tight and clean. Important things to look for include leaks or loose fittings, damaged parts, or parts out of adjustment.
Also, lock the machine’s power source and release all pressure from the compressor before performing maintenance. It is also important to keep the area around the air compressor safe by ensuring that all hoses, cables, and wires are tucked away so they are not a source of possible injury.
After starting the air compressor, perform a visual inspection of the machine to look for leaks, loose or missing parts, damaged parts, or parts out of adjustment.
9. Wear Protective Gear
Air compressors are powerful tools that must be handled with care and respect. They can pose serious risks if not properly operated and maintained. Protect yourself and others from injury by wearing appropriate protective equipment and clothing when working with air compressors.
Also, clean any hoses of dirt and debris to ensure they stay in good condition and last longer.
Finally, before installing, removing, fine-tuning, or performing any maintenance on your pneumatic impact tools or accessory parts, shut off the air source and bleed the air pressure to disengage the air hose. This helps to prevent any accidents from occurring.
10. Take Compressed Air Seriously
Air compressors can be dangerous if they are not taken seriously. High-pressure air can pose serious risks to the safety of users and surrounding areas. Knowing the risks of high-pressure air, such as damaging internal organs or causing fires, is important as a safety precaution.
It is also vital to have safety switches on air compressors that will shut off pumps when pressure is built up. To reduce the risk of injury, avoiding injecting air into the bloodstream is important, which can lead to a fatal embolism. Additionally, we must pressure-test air tanks before using them to ensure safety.
Common Hazards Of Air Compressor Tanks
As air receiver tanks, air compressor tanks are an extremely vital part of air compressor safety features. However, faulty design, improper Use, and faulty repair of the air receiver tank can result in tank failure. Therefore, following safety precautions while using air receiver tanks is vital.
Safety measures include using an OSHA-approved nozzle to reduce the risk of bodily injury due to high-pressure air release. Maintain proper air pressure in the system to prevent the nozzle from damaging or rupturing the tank and avoid leaks.
If leaks occur, immediately shut off the air supply and call safety officials.
- Do not over-pressurize or under-pressurize your system, as this can cause damage to the equipment and environment. – Never weld on air receiver tanks, as this increases the risk of rupture or explosion.
- Never repair cracks or leaks on air receiver tanks, as this increases the risk of tank failure. Thus, you must follow all safety precautions while handling air receiver tanks to ensure their safety and longevity.
Conclusion
Compressed air is a high-pressure gas that can cause serious injury or death if mishandled. Remember this when working with compressed air, and ensure you have a compressed air system safety manual.
Safety is of utmost importance when working with air compressor tanks. These safety tips will help keep you and your family and your air compressor tank safe. Air compressor tank safety is crucial for the well-being of both the user and the equipment.
Follow the mentioned safety precautions, such as checking the tank pressure, maintaining the compressor regularly, and wearing safety gear.
Operating equipment like this will go a long way in preventing accidents and extending the compressor’s lifespan. It is always better to prioritize safety measures and prevent accidents rather than risk injury or damage to property.
Frequently Asked Questions
[rank_math_rich_snippet id=”s-3456ae2b-dda5-40d0-938f-0cae24cfc079″]
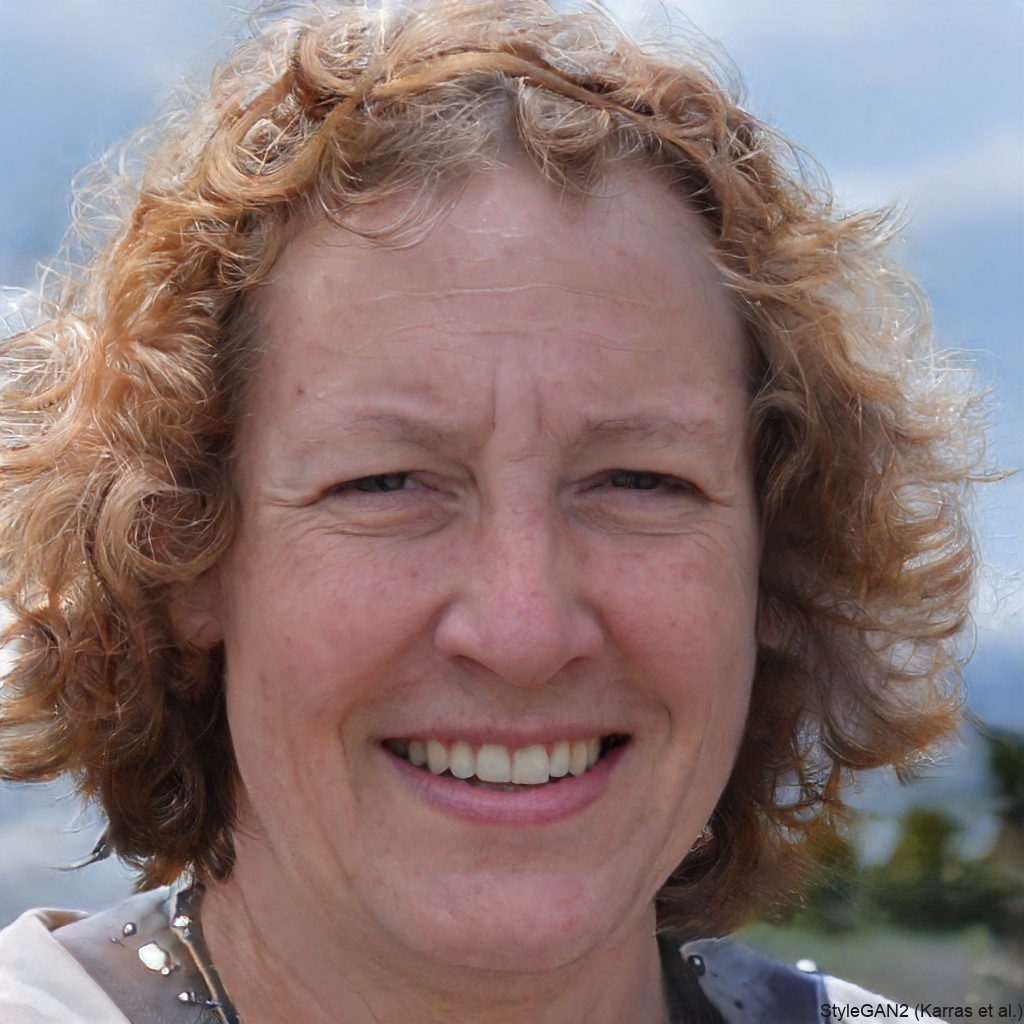
I am passionate about home engineering. I specialize in designing, installing, and maintaining heating, ventilation, and air conditioning systems. My goal is to help people stay comfortable in their homes all year long.